技術情報②
生型材料及び生型試験法の基礎(改訂版)
株式会社ツチヨシ産業 水田豊昭・黒川 豊 |
1. | 生型砂の定義 | |
2. | 生型砂構成物の役割 | |
3. | 生型砂構成物の解説 | |
1. | けい砂(Silica sand) ・けい砂とSiO2 ・けい砂の粒度と焼付き欠陥の関係 ・特殊基材 |
|
2. | ベントナイト(Bentonite) ・ベントナイトの結晶構造と吸水 ・ベントナイトの種類 ・生型鋳型の強度 ・ベントナイトの劣化と再水和 |
|
3. | 澱粉(Starch) ・澱粉の役割 ・澱粉の粘結力 ・澱粉の使用目的 ・澱粉の規格 |
|
4. | 石炭粉(Sea coal) ・石炭粉使用の目的 ・炭素質添加材の種類 |
|
5. | オーリチック(Oolitics) ・オーリチックの定義と役割 ・オーリチックの形状(SEM観察) ・オーリチックの物性と生型特性との関係 |
|
4. | 生型砂の管理法 | |
1. | 管理の頻度 | |
2. | 生型砂の測定例 | |
3. | 管理のための試験方法 ・コンパクタビリティ(Compactability) ・水 分(Moisture) ・試験片重量(密度)(Specimen weight(density)) ・抗圧力、せん断力(Green compression strength, Shearing strength) ・通気度(Permeability) ・全粘土分(Total clay) ・活性粘土分(Active clay,M.B.clay) ・灼熱減量(Loss on ignition) ・粒度分布(Grain fineness distribution) |
|
5. | シリカプログラム(Silica program) | |
1. | シリカプログラム試験における用語の意味 | |
2. | 化学分析シリカプログラム試験におけるオーリチック分の定義 | |
3. | 補正X線回折オーリチック試験法 1,2) | |
6. | 結 言 |
1.生型砂の定義
生型砂とは,けい砂,ベントナイト(bentonite),二次添加材及び水等を混練した鋳物砂である.
粘結力と適当な空隙を有しているために鋳物砂及び鋳型として利用可能となる.
けい砂(石英)は1745℃の耐熱性があるために,耐火物として注湯時に鋳型を保持する.
生型砂中におよそ60~90%存在する主基材である.
ベントナイトは主粘結剤で粘土鉱物の一種のモンモリロナイト(montmorillonite)であり,水を含有することで粘結剤となる.
その量はおよそ5~15%の範囲内で使用され,けい砂粒子を結合する.
ベントナイト量が15%以上になると生型砂中に適当な空隙が存在しなくなり,鋳物砂としての機能しなくなる.
二次添加材は必要に応じて,造型欠陥対策,鋳造欠陥対策あるいは型バラシ性改善等を目的に,石炭粉や澱粉等を添加する.
これらが生型砂の出発原料であるが,鋳造工場で繰り返し使用される生型砂は,熱影響や中子の混入あるいは繰り返し使用の結果 ,これら材料に変化が生じる.
大きく変化する点は,ベントナイトのオーリチック(oolitics)化であり不活性微粉化である.
Fig.1,Table1に,新しい生型砂と繰り返し使用した生型砂(system sand)の組成の比較をまとめた.
粘結力と適当な空隙を有しているために鋳物砂及び鋳型として利用可能となる.
けい砂(石英)は1745℃の耐熱性があるために,耐火物として注湯時に鋳型を保持する.
生型砂中におよそ60~90%存在する主基材である.
ベントナイトは主粘結剤で粘土鉱物の一種のモンモリロナイト(montmorillonite)であり,水を含有することで粘結剤となる.
その量はおよそ5~15%の範囲内で使用され,けい砂粒子を結合する.
ベントナイト量が15%以上になると生型砂中に適当な空隙が存在しなくなり,鋳物砂としての機能しなくなる.
二次添加材は必要に応じて,造型欠陥対策,鋳造欠陥対策あるいは型バラシ性改善等を目的に,石炭粉や澱粉等を添加する.
これらが生型砂の出発原料であるが,鋳造工場で繰り返し使用される生型砂は,熱影響や中子の混入あるいは繰り返し使用の結果 ,これら材料に変化が生じる.
大きく変化する点は,ベントナイトのオーリチック(oolitics)化であり不活性微粉化である.
Fig.1,Table1に,新しい生型砂と繰り返し使用した生型砂(system sand)の組成の比較をまとめた.
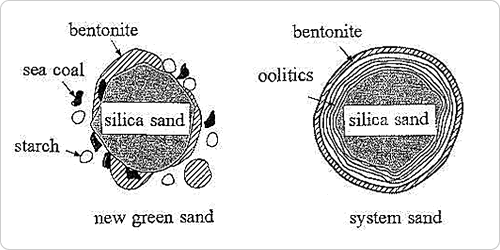
▲Fig.1 生型砂砂粒の模式図1)
Table1 生型砂の組成 |
new green sand | system sand | |
silica sand | base sand,core sand | |
bentonite moisture | bentonite,oolitics,inert fines moisture | |
sea coal | sea coal | carbonaceous material |
starch | starch | |
core binder | ||
metallics |
2.生型砂構成物の役割
Table2に生型組成物の役割と目的の一覧表を示す.
生型砂の組成で最も量が多いのは前述したようにけい砂であり,これの役割は耐火物として鋳型を保持することである.
次いで主粘結剤であるベントナイトと水,二次粘結材である澱粉と石炭粉,注湯によって生成したオーリチックや不活性微粉等である.
生型砂の組成で最も量が多いのは前述したようにけい砂であり,これの役割は耐火物として鋳型を保持することである.
次いで主粘結剤であるベントナイトと水,二次粘結材である澱粉と石炭粉,注湯によって生成したオーリチックや不活性微粉等である.
Table2 生型砂組成物の役割と目的 |
sand | 耐火物(refractory material) | |
bentonite | 主粘結剤(binder,MB-clay) | |
moisture | ベントナイト等と水和することで粘結力が発生する | |
sea coal | 焼付き欠陥対策,ピンホール(FCD)対策,崩壊性改良 | |
oolitic material | ベントナイト等が焼結し多孔質なガラス状物質としてけい砂に付着する | |
inert fines | ベントナイト等が焼結し微粉化した物がメイン. 20μ m以下でMB-clayでない物質 ,揮発成分は含まない |
|
carbonaceous material | sea coal starch core binder |
有機質の揮発成分 |
metallics | 金属ガスが鋳型中で冷却.湯玉 ,バリ等 | |
loss on ignition | 無機・有機の揮発成分 |
Fig.2は,石英量の変化と生型組成組成の例である.
石英量は鋳造欠陥と密接な関係がある.その量が少なくても多くても鋳造欠陥が発生する.
Fig.2(A)は石英量が多い例であるが,この時は鋳型が高膨張となり,すくわれ・しぼられ系の欠陥が発生しやすい.
Fig.2(B)は石英量が少ない例であり,この際は耐火度不足のために焼付き欠陥が発生しやすい.
Fig.2(C)は石英量のバランスがとれ,良好な鋳造条件となる.
以下に,それぞれの生型組成物について適正な量・使用方法について詳述する.
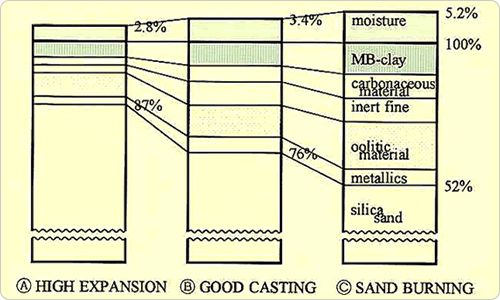
▲Fig.2 生型砂組成のモデル
3.生型砂構成物の解説
■1-けい砂(Silica sand) |
●けい砂とSiO2
けい砂は,石英(SiO2)を主成分とし,一定のサイズを持った耐火物である.
一般的にSiO2の高いけい砂は,膨張系の欠陥が発生しやすいが焼付き欠陥は発生しにくい.
生型は,主型と中子で粘結剤の種類や量が異なるために,それぞれの鋳型で要求されるけい砂のSiO2が異なる.
個々の鋳物で異なるケースが多いが,一般的には,Table3の関係になる.
けい砂は,石英(SiO2)を主成分とし,一定のサイズを持った耐火物である.
一般的にSiO2の高いけい砂は,膨張系の欠陥が発生しやすいが焼付き欠陥は発生しにくい.
生型は,主型と中子で粘結剤の種類や量が異なるために,それぞれの鋳型で要求されるけい砂のSiO2が異なる.
個々の鋳物で異なるケースが多いが,一般的には,Table3の関係になる.
Table3 鋳型の種類とSiO2の関係 |
主型用 | 中子用 | |
85%以下 | 耐火度不足 一般的には使用しがた い |
適用できる鋳物もあるが, 焼付きが発生しやすい |
85~90% | 比較的焼付きが発生しやすい | 使用可能である 低膨張基材として使用する |
90~95% | 使用可能である | 使用可能である |
95~100% | 使用可能である | 使用可能であるが,やや膨 張系の欠陥が発生しやすい |
●けい砂の粒度と焼付き欠陥の関係
けい砂のサイズは,生型用としては,AFS指数で50~100(0.30~0.15mm)が多い.
AFS指数が大きくなると,粒子サイズが大きくなる.
粒子サイズが大きい方と通気性がよく,ガス欠陥の危険性が少ないが,物理的焼付き欠陥が発生しやすく鋳肌が悪い.
Fig.3-1に溶湯ヘッド高さと平均粒子サイズの関係を示す.
平均粒子サイズが大きくなるにしたがって,ヘッド高さを低くしなければ,焼付き欠陥が発生しやすくなる.
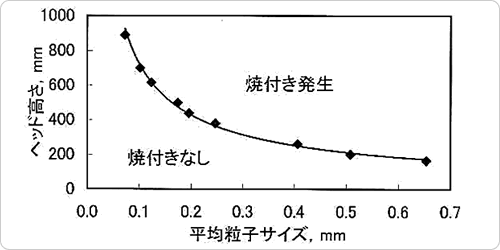
▲Fig.3-1 焼付きに対するけい砂粒度と溶湯ヘッド高さの関係*)
Fig.3-2に,溶湯と鋳型界面における焼付き欠陥の圧力バランスを示す2).
圧力バランスは(1)式に示される.さらに,(1)式の各項は(2)~(7)式により導かれる.
圧力バランスは(1)式に示される.さらに,(1)式の各項は(2)~(7)式により導かれる.

▲Fig.3-2 溶湯と鋳型界面における焼付き欠陥の圧力バランス
![]() |
Pst | :static pressure(静圧) |
Pdyn | :dynamic pressure(動圧) |
Pexp | :expansion during solidification(only for cast iron)(凝固膨張) |
Pγ | :capillary pressure(毛細管圧) |
Pf | :friction between the liquid metal and the sand grains(鋳型溶湯間の摩擦力) |
Pgas | :pressure resulting from the expansion of the mold gasses(鋳型背圧) |
![]() |
γLV | :liquid metal/vapor surface energy(液体金属及び蒸気の表面エネルギー) |
de | :average pore opening between sand grains(砂粒子の平均空隙) |
θ | :contact angle(接触角) |
![]() |
γSV | :solid metal/vapor surface energy(固体金属及び蒸気の表面エネルギー) |
γLS | :liquid metal/vapor surface energy(液体金属及び蒸気の表面エネルギー) |
![]() |
μ | :viscosity of the liquid metal(液体金属の粘性) |
K | :permeability of the molding sand(鋳型の通気度) |
Lp | :length through which the liquid flows(depth of penetration)(焼付き深さ) |
Vp | :speed with which the metal moves through the sand(鋳型内の金属移動速度) |
![]() |
fd | :fractional density of the molding sand(鋳型密度) |
d | :average grain diameter(砂粒子の平均直径) |
![]() |
ρ | :density of the alloy(金属の密度) |
g | :gravitational acceleration(重力加速度) |
h | :height of the metal in the mold(溶湯のヘッド高さ) |
![]() |
V | :velocity of the metal that hits the mold wall(金属の粘性) |
溶湯と鋳型界面における焼付き欠陥の圧力バランスは,溶湯側から働く圧力Pst(静圧),Pdyn(動圧),Pexp(凝固膨張)と,鋳型側から働く圧力Pγ(毛細管圧),Pf(鋳型溶湯間の摩擦力),Pgas(鋳型背圧)に左右される.
砂粒子の大きさは,主にPγ(毛細管圧)により圧力バランスに影響する.
(2)式において,砂粒子が大きくなることで,de(砂粒子の平均空隙)が増加しPγ(毛細管圧)が低下する.
なお,(2)式におけるcosθ(接触角)は通常,θ>90°であり、cosθ(接触角)はマイナスとなり,Pγ(毛細管圧)はプラスとなる.ただし,θ<90°では、cosθ(接触角)はプラスとなり,Pγ(毛細管圧)はマイナスとなる.
θ<90°となる条件は,鋳型内部に低粘性スラグの生成,けい砂の溶融,低融点物質の生成した場合である.cosθ(接触角)の概念図はFig.3-3に示す
また,けい砂の種類によって,接触角は変化する.
Fig.3-4にけい砂及び特殊砂の各C値における接触角を示す.
けい砂は接触角が低いために焼付きが発生しやすい傾向にあるが,カーボンサンド,クロマイトサンド,ジルコンサンドは順次,接触角が高くなり,焼付きが発生しがたいと言える.
砂粒子の大きさは,主にPγ(毛細管圧)により圧力バランスに影響する.
(2)式において,砂粒子が大きくなることで,de(砂粒子の平均空隙)が増加しPγ(毛細管圧)が低下する.
なお,(2)式におけるcosθ(接触角)は通常,θ>90°であり、cosθ(接触角)はマイナスとなり,Pγ(毛細管圧)はプラスとなる.ただし,θ<90°では、cosθ(接触角)はプラスとなり,Pγ(毛細管圧)はマイナスとなる.
θ<90°となる条件は,鋳型内部に低粘性スラグの生成,けい砂の溶融,低融点物質の生成した場合である.cosθ(接触角)の概念図はFig.3-3に示す
また,けい砂の種類によって,接触角は変化する.
Fig.3-4にけい砂及び特殊砂の各C値における接触角を示す.
けい砂は接触角が低いために焼付きが発生しやすい傾向にあるが,カーボンサンド,クロマイトサンド,ジルコンサンドは順次,接触角が高くなり,焼付きが発生しがたいと言える.
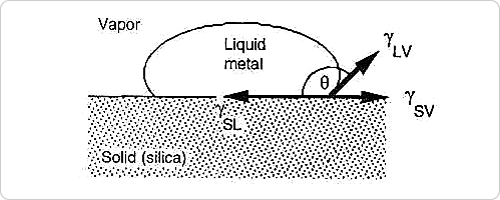
▲Fig.3-3 接触角の概念図
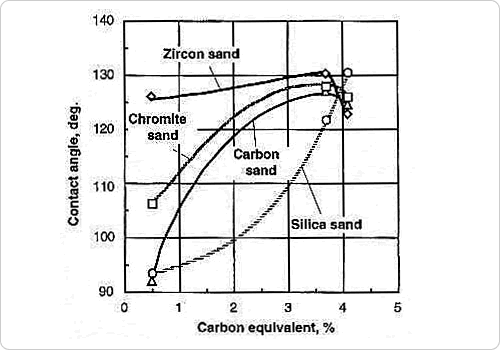
▲Fig.3-4 鋳物砂の種類と溶湯接触角の関係
●特殊基材
けい砂以外の生型基材として,ジルコンサンド(Zircon sand),クロマイトサンド(Chromite sand),オリビンサンド(Olivine sand),ムライトサンド(Mullite sand)等が使用される.
これらの使用目的で共通 している点は,低膨張基材としてのすくわれ・しぼられ欠陥対策である.
また,ムライトサンド以外はけい砂と比較して熱伝導性や接触角が高くいために,鋳型-溶湯界面 で発生する欠陥(焼付き欠陥,ガス欠陥)防止に効果がある.
さらに,オリビンサンドは,塩基性であるために,酸化雰囲気で発生しやすいファイアライト(2FeO・SiO2)生成による化学的な焼付き欠陥防止に効果的である.
けい砂以外の生型基材として,ジルコンサンド(Zircon sand),クロマイトサンド(Chromite sand),オリビンサンド(Olivine sand),ムライトサンド(Mullite sand)等が使用される.
これらの使用目的で共通 している点は,低膨張基材としてのすくわれ・しぼられ欠陥対策である.
また,ムライトサンド以外はけい砂と比較して熱伝導性や接触角が高くいために,鋳型-溶湯界面 で発生する欠陥(焼付き欠陥,ガス欠陥)防止に効果がある.
さらに,オリビンサンドは,塩基性であるために,酸化雰囲気で発生しやすいファイアライト(2FeO・SiO2)生成による化学的な焼付き欠陥防止に効果的である.
■2-ベントナイト(Bentonite) |
●ベントナイトの結晶構造と吸水
ベントナイトは,Fig.4の結晶構造を持った粘土鉱物である.
シリカ4面体-アルミナ8面体-シリカ4面体による3層構造であり,2:1型の粘土鉱物である.
ベントナイトの粘結力は,結晶層が電荷を帯びていることにある.
この原因は,主にアルミナ8面体のAl3+が電荷の低いMg2+に同型置換することで,陽電荷が不足することにある.
そして,層間に交換性陽イオン吸着されて存在している.
結晶層の陰イオンと交換性陽イオンに働くクーロン力(F∝q・q′/r2 ここにF:クーロン力,q,q′:電荷,r:距離)によってベントナイトの粘結力が発現する.
このクーロン力は水が結晶層の層間に配列することで働く.
Fig.5に砂粒子にコーティングしたベントナイトの吸水による特性変化を示す.
層間に水が3分子入ると最大の抗圧力となり,4分子入ると鋳型密度が最も低くなる.
ベントナイトは,Fig.4の結晶構造を持った粘土鉱物である.
シリカ4面体-アルミナ8面体-シリカ4面体による3層構造であり,2:1型の粘土鉱物である.
ベントナイトの粘結力は,結晶層が電荷を帯びていることにある.
この原因は,主にアルミナ8面体のAl3+が電荷の低いMg2+に同型置換することで,陽電荷が不足することにある.
そして,層間に交換性陽イオン吸着されて存在している.
結晶層の陰イオンと交換性陽イオンに働くクーロン力(F∝q・q′/r2 ここにF:クーロン力,q,q′:電荷,r:距離)によってベントナイトの粘結力が発現する.
このクーロン力は水が結晶層の層間に配列することで働く.
Fig.5に砂粒子にコーティングしたベントナイトの吸水による特性変化を示す.
層間に水が3分子入ると最大の抗圧力となり,4分子入ると鋳型密度が最も低くなる.
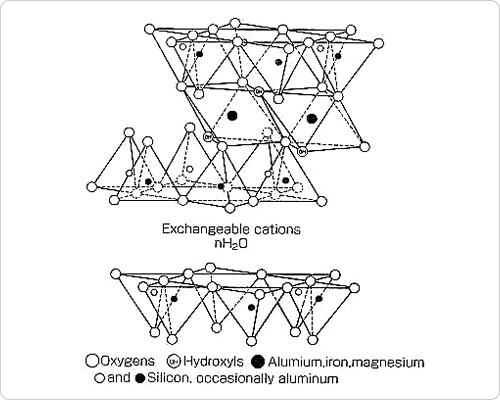
▲Fig.4 ベントナイト結晶層の模式図3)
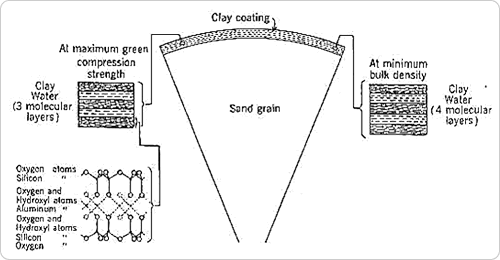
▲Fig.5 砂粒にコーティングしたベントナイトの吸水による特性変化の模式図4)
●ベントナイトの種類
鋳造用ベントナイトには3タイプある.
Fig.4の交換性陽イオンがNa+あるいはCa2+によりNaベントナイト,Caベントナイトに分かれる.
活性化ベントナイトは,Caベントナイトに炭酸ナトリウム(Na2CO3)を添加して交換性陽イオンをNa+に変更したベントナ イトである.
3タイプのベントナイトの特徴をTable4に示す.
鋳造用としては,Naベントナイトが主に使用さる.
崩壊性や混練性の改善のために,Naベントナイトに活性化ベントナイトをブレンドすることがある.
Caベントナイトは,鋳造用としては日本ではあまり使用されない.
ベントナイトのタイプによって,Table4のように鋳型特性異なる.
また,市販のベントナイトは産地によって,モンモリロナイト純度が異なる.
そのために,Table4のタイプ別の分類が当てはまらないケースが多い.
したがって,ベントナイトを選ぶ際には,個々のベントナイトの特性を十分に理解して選ぶ必要がある.
●生型鋳型の強度
生型砂の強度は,ベントナイトの粘結力に主に起因するが,これ以外に,けい砂の摩擦応力も重要な役目を果たす.
Fig.6に,コンパクタビリティ(compactability)と湿態抗圧力 の関係を示す.
鋳造用ベントナイトには3タイプある.
Fig.4の交換性陽イオンがNa+あるいはCa2+によりNaベントナイト,Caベントナイトに分かれる.
活性化ベントナイトは,Caベントナイトに炭酸ナトリウム(Na2CO3)を添加して交換性陽イオンをNa+に変更したベントナ イトである.
3タイプのベントナイトの特徴をTable4に示す.
鋳造用としては,Naベントナイトが主に使用さる.
崩壊性や混練性の改善のために,Naベントナイトに活性化ベントナイトをブレンドすることがある.
Caベントナイトは,鋳造用としては日本ではあまり使用されない.
Table4 3タイプのベントナイトの特徴 |
sodium bentonite | calcium bentonite | active bentonite | |
mixing time | long | short | short |
green compression by short mixing | low | high | high |
green compression by long mixing | high | middle | middle |
dry compression | high | low | middle |
loss on heating | low | high | middle |
scab resistance | good | bad | middle |
collapsibility | bad | good | good |
ベントナイトのタイプによって,Table4のように鋳型特性異なる.
また,市販のベントナイトは産地によって,モンモリロナイト純度が異なる.
そのために,Table4のタイプ別の分類が当てはまらないケースが多い.
したがって,ベントナイトを選ぶ際には,個々のベントナイトの特性を十分に理解して選ぶ必要がある.
●生型鋳型の強度
生型砂の強度は,ベントナイトの粘結力に主に起因するが,これ以外に,けい砂の摩擦応力も重要な役目を果たす.
Fig.6に,コンパクタビリティ(compactability)と湿態抗圧力 の関係を示す.
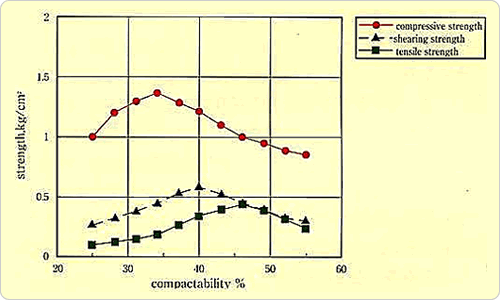
▲Fig.6 生型砂の抗圧力,せん断力,引張力の関係
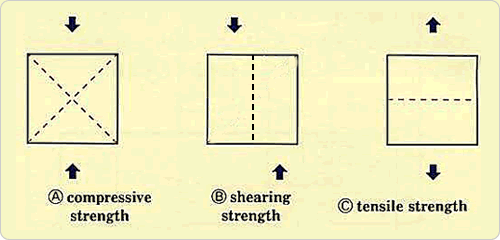
▲Fig.7 生型試験片における抗圧力,せん断力,引張力試験の荷重
Fig.6において,抗圧力は低コンパクタビリティで最大値になり,せん断力及び引張力は高コンパクタビリティ側に最大値のピークが変化する.
これは,ベントナイトの粘結力とけい砂の摩擦応力の関係で説明できる.
Fig.7のモデルから分かるように,抗圧力の場合は,けい砂のずり応力が働くために摩擦応力の寄与率が高くなる.
引張力で測定時に,けい砂の摩擦の影響をあまり受けないので,ベントナイトの粘結力の寄与率が高くなる.せん断力はそれらの中間である.
●ベントナイトの劣化と再水和
Fig.8にベントナイトの熱劣化と再水和による回復を示した.
ベントナイトは,熱により徐々に劣化し,700℃以上では粘結力が無くなる.
ベントナイトの熱劣化は,200~600℃における層間水の脱水による劣化,600~700℃以上における結晶構造の破壊による劣化,の2種類がある.
結晶構造の破壊による劣化は回復させることは不可能であるが,層間水の 脱水による劣化は再水和によってある程度の回復が可能である.
この再水和による回復は,"熟成:the temper of system sand"という現象で,鋳造工場ではよく知られている.
これは,ベントナイトの粘結力とけい砂の摩擦応力の関係で説明できる.
Fig.7のモデルから分かるように,抗圧力の場合は,けい砂のずり応力が働くために摩擦応力の寄与率が高くなる.
引張力で測定時に,けい砂の摩擦の影響をあまり受けないので,ベントナイトの粘結力の寄与率が高くなる.せん断力はそれらの中間である.
●ベントナイトの劣化と再水和
Fig.8にベントナイトの熱劣化と再水和による回復を示した.
ベントナイトは,熱により徐々に劣化し,700℃以上では粘結力が無くなる.
ベントナイトの熱劣化は,200~600℃における層間水の脱水による劣化,600~700℃以上における結晶構造の破壊による劣化,の2種類がある.
結晶構造の破壊による劣化は回復させることは不可能であるが,層間水の 脱水による劣化は再水和によってある程度の回復が可能である.
この再水和による回復は,"熟成:the temper of system sand"という現象で,鋳造工場ではよく知られている.
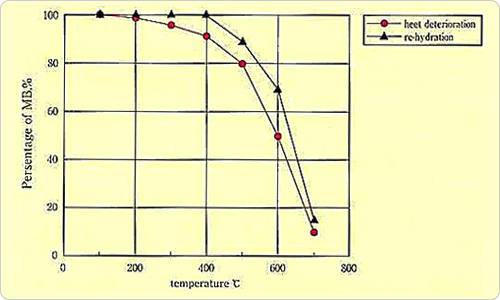
▲Fig.8 ベントナイトの熱劣化と再水和
■3-澱粉(Starch) |
●澱粉の役割
澱粉はベントナイトの補助粘結剤として,以下の3点の目的で使用される.
(1)砂かみ防止(protect of sand inclusions)
(2)すくわれ防止(protect of scab)
(3)型落ち対策(protect of mold drop).
澱粉は,粘結剤として働き,引張力を改善する効果がある.
抗圧力を改善する度合いは低い.
Fig.9に,澱粉で防止できる鋳造欠陥のモデルを示す.
したがって,Fig.9のモデル(C)におけるような引張り応力が鋳型に加わる場合, その応力に耐える効果がある.
砂かみ欠陥の場合,砂粒が鋳型から剥離する現象であるために,澱粉で防止可能である.
すくわれ欠陥は鋳型の一部が膨張で層状となってめくれ上がる現象である.
層状の鋳型の剥離を止める効果 が澱粉にある.
また,澱粉は,焼結した鋳型内ではクッション材の役目を果たし膨張を緩和して,焼結層が剥離する力を弱める.
型落ちは,引張力の増加によって, 鋳型の落下を防止する.
また,模型と鋳型面では滑りの効果があり,離型の際の力を小さくする.
澱粉はベントナイトの補助粘結剤として,以下の3点の目的で使用される.
(1)砂かみ防止(protect of sand inclusions)
(2)すくわれ防止(protect of scab)
(3)型落ち対策(protect of mold drop).
澱粉は,粘結剤として働き,引張力を改善する効果がある.
抗圧力を改善する度合いは低い.
Fig.9に,澱粉で防止できる鋳造欠陥のモデルを示す.
したがって,Fig.9のモデル(C)におけるような引張り応力が鋳型に加わる場合, その応力に耐える効果がある.
砂かみ欠陥の場合,砂粒が鋳型から剥離する現象であるために,澱粉で防止可能である.
すくわれ欠陥は鋳型の一部が膨張で層状となってめくれ上がる現象である.
層状の鋳型の剥離を止める効果 が澱粉にある.
また,澱粉は,焼結した鋳型内ではクッション材の役目を果たし膨張を緩和して,焼結層が剥離する力を弱める.
型落ちは,引張力の増加によって, 鋳型の落下を防止する.
また,模型と鋳型面では滑りの効果があり,離型の際の力を小さくする.
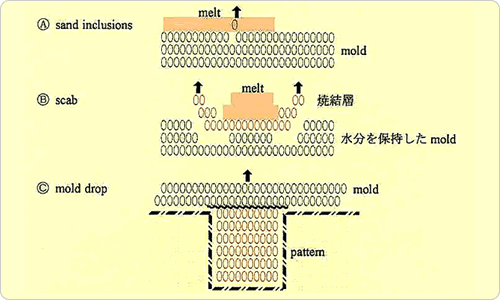
▲Fig.9 澱粉で防止できる鋳造欠陥のモデル
●澱粉の粘結力
澱粉は,主として分枝状のアミロペクチンがミセルを形成している.
α澱粉では,Fig.10に示したように,ミセル内に水分子が進入することで,膨潤し粘りのある糊となって粘結力が発現する.
Fig.10に澱粉の粘結機構を示す.
分枝状のアミロペクチンが複雑なネットワークとなり,粘結力が発現するために,ベントナイトとは異なる粘結力で,せん断力や引張力に対して抵抗が高くなる.
澱粉は,主として分枝状のアミロペクチンがミセルを形成している.
α澱粉では,Fig.10に示したように,ミセル内に水分子が進入することで,膨潤し粘りのある糊となって粘結力が発現する.
Fig.10に澱粉の粘結機構を示す.
分枝状のアミロペクチンが複雑なネットワークとなり,粘結力が発現するために,ベントナイトとは異なる粘結力で,せん断力や引張力に対して抵抗が高くなる.
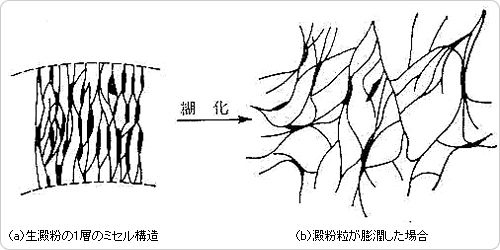
▲Fig.10 澱粉の粘結機構5)
●澱粉の使用目的
澱粉は,ベントナイトの粘結力を補完するために二次粘結材であり,添加する必要が生じたときに使用すればよい.
ところが,以下の理由で,最近の生型砂には澱粉添加の必要性が増している.
●高速造型機の普及で,流動性のよい生型砂が好まれる様になってきた結果,低コンパクタビリティの生型砂が多くなってきた.
→表面安定性が低下気味になり,これを改善するために澱粉が使用されるようになった.
●静圧,インパクト造型機により,高充填鋳型が得られる様になり,鋳型の抜型抵抗が増加してきた.また,これらの造型機では固有のブリッジ現象のために型落ちが発生しやすくなった.
→ 抜型抵抗,離型抵抗の増加のために澱粉が使用されるようになった.
●高充填鋳型のために,従来の中~高圧造型機では発生しないすくわれ・しぼられ欠陥が増加してきた.
→ 耐すくわれ・しぼられ性の改善のために澱粉が使用されるようになってきた.
澱粉の添加量は,造型欠陥や鋳造欠陥の発生状況により変化させることが原則である.
ただし,あまり多量に添加すると生型砂の流動性・充填性が悪化する.
そのために,残存澱粉量で0.5~1.0%を越えないで使用することが一般的である.
ただし,例外的に鋳鋼では,すくわれ,砂かみ対策から残存澱粉1.0~1.5%で使用されている.
残存澱粉に範囲があるのは,澱粉の品位の差から来るものである.
鋳造用澱粉として市販されている澱粉の 品位は種々ある.
澱粉価,α化度等により澱粉の品位を判定できる.
市販の澱粉の中には品位の低いもの(クッション材の効果として使用されるようなケース)もあり,その場合は,流動性・充填性の阻害効果が低いために残存澱粉量が高くなる.
高品位澱粉では,残 存澱粉量は0.5%程度が限界である.
澱粉添加量は,ベントナイト添加量に対して5~10%%が多く,対ベントナイト10%添加で残存澱粉量が0.3~0.5%になる(高品位澱粉)ことが多い.
●澱粉の規格
鋳物用澱粉は,コーン,小麦,コメ,イモ等が色々あり物性も異なる.
Table5に試験方法を示す.
市販の鋳造澱粉は数々あるので,規格からその品位を推定する必要がある.
以下に示す規格が一般的な鋳造用澱粉の規格である.
澱粉は,ベントナイトの粘結力を補完するために二次粘結材であり,添加する必要が生じたときに使用すればよい.
ところが,以下の理由で,最近の生型砂には澱粉添加の必要性が増している.
●高速造型機の普及で,流動性のよい生型砂が好まれる様になってきた結果,低コンパクタビリティの生型砂が多くなってきた.
→表面安定性が低下気味になり,これを改善するために澱粉が使用されるようになった.
●静圧,インパクト造型機により,高充填鋳型が得られる様になり,鋳型の抜型抵抗が増加してきた.また,これらの造型機では固有のブリッジ現象のために型落ちが発生しやすくなった.
→ 抜型抵抗,離型抵抗の増加のために澱粉が使用されるようになった.
●高充填鋳型のために,従来の中~高圧造型機では発生しないすくわれ・しぼられ欠陥が増加してきた.
→ 耐すくわれ・しぼられ性の改善のために澱粉が使用されるようになってきた.
澱粉の添加量は,造型欠陥や鋳造欠陥の発生状況により変化させることが原則である.
ただし,あまり多量に添加すると生型砂の流動性・充填性が悪化する.
そのために,残存澱粉量で0.5~1.0%を越えないで使用することが一般的である.
ただし,例外的に鋳鋼では,すくわれ,砂かみ対策から残存澱粉1.0~1.5%で使用されている.
残存澱粉に範囲があるのは,澱粉の品位の差から来るものである.
鋳造用澱粉として市販されている澱粉の 品位は種々ある.
澱粉価,α化度等により澱粉の品位を判定できる.
市販の澱粉の中には品位の低いもの(クッション材の効果として使用されるようなケース)もあり,その場合は,流動性・充填性の阻害効果が低いために残存澱粉量が高くなる.
高品位澱粉では,残 存澱粉量は0.5%程度が限界である.
澱粉添加量は,ベントナイト添加量に対して5~10%%が多く,対ベントナイト10%添加で残存澱粉量が0.3~0.5%になる(高品位澱粉)ことが多い.
●澱粉の規格
鋳物用澱粉は,コーン,小麦,コメ,イモ等が色々あり物性も異なる.
Table5に試験方法を示す.
市販の鋳造澱粉は数々あるので,規格からその品位を推定する必要がある.
以下に示す規格が一般的な鋳造用澱粉の規格である.
水分 | :5~15% |
粒度 | :45MESH以下 95%以上 |
α化度 | :80~100% |
膨潤度 | :50%以上 |
粗蛋白 | :0~10% |
粗繊維 | :0~20% |
Table5 澱粉の試験方法 |
試験方法 | 備 考 | |
水分 | 100℃乾燥法 | 10%前後が目安である.20%以上では,保存中に劣化しベータ(β)化が進行する.5%以下では混練に支障をきす.5~15%が適当である. |
粒度 | ロータップ法 | 45MESH以下95%以上が適当である.粗いと澱粉の効果が期待できない.混練が難しくなる.細かいほど良好である. |
α化度 | ジアスターゼ法 | 00%に近い程,鋳造用澱粉として良好である.ただし,この試験は,鋳造用澱粉に澱粉以外の物が入っていても,澱粉のα化度が高ければ,高くなる. |
膨潤度 | メスシリンダ法 | 50%以上で,良好である.簡易α化度試験とも言われる.この試験法は,同一組成の鋳造用澱粉なら,βから,αになるにしたがってリニアに増加する.澱粉の種類,組成が変化すると比較できない. |
粗蛋白 | ケルダール法 | 蛋白が多いと,保存性(腐食),窒素欠陥の問題がある.しかし,蛋白は粘性があるので,表面安定性改善には効果がある.粗蛋白は0~10%が適当である. |
粗繊維 | 静置法 | 繊維は,クッション材としての役目と流動性改善の役目がある.しかし,粘性はないので鋳物砂の粘りは期待できない.0~20%が適当である. |
■4-石炭粉(Sea coal) |
●石炭粉使用の目的
石炭粉の使用目的は,以下の3点である.
(1)焼付き,目さし対策(protect of burn and penetration)
(2)FCDのピンホール対策(protect of pinholes(FCD))
(3)シェイクアウトの崩壊性改良(collapsibility)
石炭粉の添加により,ガスフィルムやラストラスカーボンの生成による溶湯の濡れ性(接触角)の改善により欠陥が防止できる.
(1)焼付き欠陥対策
物理的な焼付き欠陥防止に対しては,鋳型から発生するガスフィルムが背圧となって焼付きを防止する説,発生するラストラスカーボンが鋳型-溶湯界面に存在することで焼付きを防止する説の2説がある.
化学的な焼付き欠陥に対しては,還元雰囲気でファイアライト生成を抑制するとされている.
還元雰囲気では溶湯が酸化しにくいために,ファイアライト生成につながりにくい.
Fe+O→FeO
2FeO+SiO2→2FeO・SiO2
(2)FCDのピンホール対策
FCDでは特有のドロス欠陥と称されるガス欠陥が発生しやすい.
以下の反応式により水素が放出されてガス欠陥となるが,石炭粉の使用により鋳型が還元性となり,MgO生成を抑制することで,ガス欠陥が防止される.
FCDのガス欠陥は,外観が球状であり,内部には炭化物が観察される.
SEMを用いて観察すると特徴的なために判定しやすい6).
MgC2+H2O→MgO+C2H2
C2H2→2C+H2
(3)シェイクアウトの崩壊性改良
上記(2)と同様の理由により,鋳型-溶湯界面の分離が容易になり,シェイクアウトが容易になる.
●炭素質添加材の種類
石炭粉とは石炭(弱粘結炭)を原料とした炭素質の添加材であるが,石炭粉以外の炭素質材料としては,ギルソナイト(天然に産する物と石油より精製されるアスファルト系の物がある),ピッチ(石炭及び石油より精製される),黒鉛粉(天然黒鉛と人造黒鉛がある)等がある.
鋳造工場での使用は,石炭粉が圧倒的に多く,他の物は極僅かに使用されている程度である.
Table6に,石炭粉とギルソナイトの分析例を示す.
ギルソナイトは揮発分が多く,そのために生成するラストラスカーボンも多いが,使用に当たっては添加量に注意をしないとブローホールが発生する例もある.
石炭粉の使用目的は,以下の3点である.
(1)焼付き,目さし対策(protect of burn and penetration)
(2)FCDのピンホール対策(protect of pinholes(FCD))
(3)シェイクアウトの崩壊性改良(collapsibility)
石炭粉の添加により,ガスフィルムやラストラスカーボンの生成による溶湯の濡れ性(接触角)の改善により欠陥が防止できる.
(1)焼付き欠陥対策
物理的な焼付き欠陥防止に対しては,鋳型から発生するガスフィルムが背圧となって焼付きを防止する説,発生するラストラスカーボンが鋳型-溶湯界面に存在することで焼付きを防止する説の2説がある.
化学的な焼付き欠陥に対しては,還元雰囲気でファイアライト生成を抑制するとされている.
還元雰囲気では溶湯が酸化しにくいために,ファイアライト生成につながりにくい.
Fe+O→FeO
2FeO+SiO2→2FeO・SiO2
(2)FCDのピンホール対策
FCDでは特有のドロス欠陥と称されるガス欠陥が発生しやすい.
以下の反応式により水素が放出されてガス欠陥となるが,石炭粉の使用により鋳型が還元性となり,MgO生成を抑制することで,ガス欠陥が防止される.
FCDのガス欠陥は,外観が球状であり,内部には炭化物が観察される.
SEMを用いて観察すると特徴的なために判定しやすい6).
MgC2+H2O→MgO+C2H2
C2H2→2C+H2
(3)シェイクアウトの崩壊性改良
上記(2)と同様の理由により,鋳型-溶湯界面の分離が容易になり,シェイクアウトが容易になる.
●炭素質添加材の種類
石炭粉とは石炭(弱粘結炭)を原料とした炭素質の添加材であるが,石炭粉以外の炭素質材料としては,ギルソナイト(天然に産する物と石油より精製されるアスファルト系の物がある),ピッチ(石炭及び石油より精製される),黒鉛粉(天然黒鉛と人造黒鉛がある)等がある.
鋳造工場での使用は,石炭粉が圧倒的に多く,他の物は極僅かに使用されている程度である.
Table6に,石炭粉とギルソナイトの分析例を示す.
ギルソナイトは揮発分が多く,そのために生成するラストラスカーボンも多いが,使用に当たっては添加量に注意をしないとブローホールが発生する例もある.
Table6 石炭粉とギルソナイトの分析例 |
水分 % | 揮発分 % | 灰分 % | 固定炭素 % | |
石炭粉 | 1.13 | 44.85 | 2.67 | 51.35 |
ギルソナイト | 0.37 | 81.62 | 1.62 | 16.39 |
■5-オーリチック(Oolitics) |
●オーリチックの定義と役割
オーリチックとは,主にベントナイトの焼結物がポーラスなガラス状物質となってけい砂にコーティングしたものである7,8).
ベントナイト焼結物以外に石炭粉,けい砂粉や澱粉の灰分,中子粘結剤の残留成分などから成り立っている.
その役割は,保水性の改善とクッション作用である.
ポーラスなオーリチックはその内部に水分を取り込み,生型砂を乾き難くしている.
また,オーリチックは注湯時に軟化溶融して,けい砂の膨張を緩和し,すくわれ・しぼられ欠陥防止に寄与する.
●オーリチックの形状(SEM観察)
Fig.11にけい砂断面のSEM像を示す.
Fig.11(a)はオーリチックがあまり付着していない例であり,Fig.11(b)はオーリチックが多く付着した例である.
これらのSEM像は,全粘土分を除去したオーリチック付着砂を樹脂に埋め込み,切断・研磨後に金蒸着しSEMで観察したものである.
鋳造工場で使用される生型砂はFig.11(a)の砂粒が多く,20~30粒に1粒程度Fig.11(b)の砂粒が付着しているようである.
Fig.11(a)では,砂粒の局部に薄片状にオーリチックが付着している.
Fig.11(b)ではポーラスにオーリチックが砂粒全体に発達し,あたかも擬似砂粒のようである.
オーリチックとは,主にベントナイトの焼結物がポーラスなガラス状物質となってけい砂にコーティングしたものである7,8).
ベントナイト焼結物以外に石炭粉,けい砂粉や澱粉の灰分,中子粘結剤の残留成分などから成り立っている.
その役割は,保水性の改善とクッション作用である.
ポーラスなオーリチックはその内部に水分を取り込み,生型砂を乾き難くしている.
また,オーリチックは注湯時に軟化溶融して,けい砂の膨張を緩和し,すくわれ・しぼられ欠陥防止に寄与する.
●オーリチックの形状(SEM観察)
Fig.11にけい砂断面のSEM像を示す.
Fig.11(a)はオーリチックがあまり付着していない例であり,Fig.11(b)はオーリチックが多く付着した例である.
これらのSEM像は,全粘土分を除去したオーリチック付着砂を樹脂に埋め込み,切断・研磨後に金蒸着しSEMで観察したものである.
鋳造工場で使用される生型砂はFig.11(a)の砂粒が多く,20~30粒に1粒程度Fig.11(b)の砂粒が付着しているようである.
Fig.11(a)では,砂粒の局部に薄片状にオーリチックが付着している.
Fig.11(b)ではポーラスにオーリチックが砂粒全体に発達し,あたかも擬似砂粒のようである.
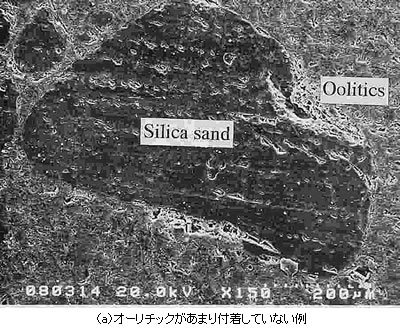
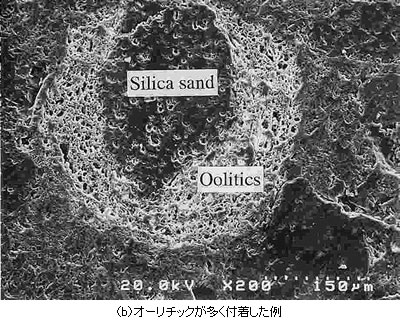
▲Fig.11 オーリチック付着砂の断面写真
●オーリチックの物性と生型特性との関係
Table7にオーリチックの水分率と比重を示す.
生型砂におけるオーリチックの役割は,前述したように保水性改善とクッション作用が主である.
保水性については,オーリチックの水分率に見られるように,オーリチックは3~10%の水分を吸着する.
クッション性については比重の低い(体積が相対的に大きい,また空隙まで含めた見かけ容積はさらに大きい)オーリチックがけい砂に付着し,約900℃で軟化溶融することで,鋳型が低膨張となる.
さらに,オーリチック付着砂は,しわ状の表面状態により,オーリチックとベン トナイトゲルの接着力が増加し,抗圧力や表面安定性の増加につながる9).
Table7にオーリチックの水分率と比重を示す.
生型砂におけるオーリチックの役割は,前述したように保水性改善とクッション作用が主である.
保水性については,オーリチックの水分率に見られるように,オーリチックは3~10%の水分を吸着する.
クッション性については比重の低い(体積が相対的に大きい,また空隙まで含めた見かけ容積はさらに大きい)オーリチックがけい砂に付着し,約900℃で軟化溶融することで,鋳型が低膨張となる.
さらに,オーリチック付着砂は,しわ状の表面状態により,オーリチックとベン トナイトゲルの接着力が増加し,抗圧力や表面安定性の増加につながる9).
Table7 オーリチックの水分率と比重(1000℃焼成オーリチック付着砂) |
A | B | (A/B)×100 | オーリチックの 比重 |
||
オーリチックの 水分量 % |
オーリチック分 % |
オーリチックの 水分率 % |
|||
ベントナイト 種類 各8%添加 |
Na,Bt-1 | 0.57 | 6.2 | 9.2 | 0.328 |
Ca,Bt | 0.16 | 5.2 | 3.1 | 0.263 | |
activate Bt | 0.47 | 6.0 | 7.8 | 0.384 | |
Na,Bt-2 | 0.42 | 6.5 | 6.5 | 0.382 | |
澱粉添加 | 0.5% | 0.58 | 6.4 | 9.1 | 0.379 |
1.0% | 0.60 | 6.2 | 9.7 | 0.314 | |
1.5% | 0.62 | 6.7 | 9.3 | ----- | |
石炭粉添加 | 1.0% | 0.62 | 6.4 | 9.7 | 0.324 |
3.0% | 0.68 | 7.3 | 9.3 | 0.381 | |
5.0% | 0.75 | 7.3 | 10.0 | 0.398 |
4.生型砂の管理法
■1-管理の頻度 |
生型砂管理の目的は,鋳造欠陥を減少させ安定して操業することにある.
生型砂管理のための試験方法は幾つかあるが,できるだけ少ない試験で最大の効果が得られるように, 試験項目を選定しなければならない.
Table8に,砂試験項目と理想的な頻度をまとめた.
また,最近は測定の自動化が進んでおり,水分,CB,抗圧力及び通気度等が1バッチ毎測定することも可能である.
自動あるいは手動で計測されたデータはコンピュータにより,演算処理され,オンラインあるいはオフラインで水分や添加剤の切り出し量にフィードバックされる.
また,傾向管理により生型砂の変動を予想し,適切な値に維持管理することが一般的になっている.
個々の試験項目について,測定原理とその目的及び管理値等について以下に詳述する.
生型砂管理のための試験方法は幾つかあるが,できるだけ少ない試験で最大の効果が得られるように, 試験項目を選定しなければならない.
Table8に,砂試験項目と理想的な頻度をまとめた.
また,最近は測定の自動化が進んでおり,水分,CB,抗圧力及び通気度等が1バッチ毎測定することも可能である.
自動あるいは手動で計測されたデータはコンピュータにより,演算処理され,オンラインあるいはオフラインで水分や添加剤の切り出し量にフィードバックされる.
また,傾向管理により生型砂の変動を予想し,適切な値に維持管理することが一般的になっている.
個々の試験項目について,測定原理とその目的及び管理値等について以下に詳述する.
Table8 生型試験法とその実施頻度 |
sand control tests | frequency |
compactability | daily test automatic test,1回/時 |
moisture | daily test automatic test,1回/時 |
specimen weight(density) | daily test 1回/時 |
green compression | daily test automatic test,1回/時 |
shearing strength | daily test 1回/時 |
permeability | daily test automatic test,1回/時 |
total clay | daily test 1回/shift |
M.B. clay | daily test 1回/shift |
loss on ignition | daily test 1回/日 |
grain fineness distribution | daily test 1回/日 |
silica program test | monthly test |
■2-生型砂の測定例 |
Table9に,弊社が測定している生型砂(約100ライン)の1985年と2006年の平均・偏差を示す10).
これらの測定は,鋳造工場より生型砂をビニール袋で頂き,数日後に弊社の試験室で測定したものである.
各々の鋳造工場の生型砂分析データをTable9と対比すれば,平均に対してどのような偏りの生型砂を使用しているか判断できる.
生型ライン構成や鋳造製品等によって,生型砂の管理値が変化するので,その偏りから理論的に妥当な生型砂かどうか判断するとよい.
なお,後述するように,オーリチック分はシリカプログラム試験ではリン酸可溶分として定量され,新のオーリチック分が測定できないので,長石を含む低耐火度 物質として表している.
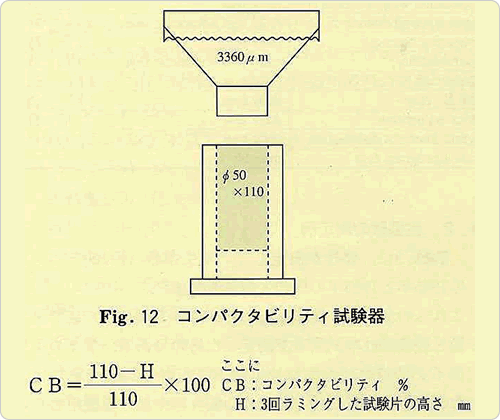
▲Fig.12 コンパクタビリティ試験器
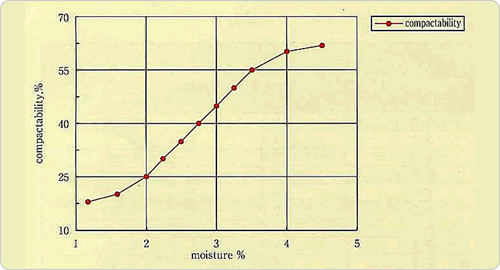
▲Fig.13 コンパクタビリティと水分の関係
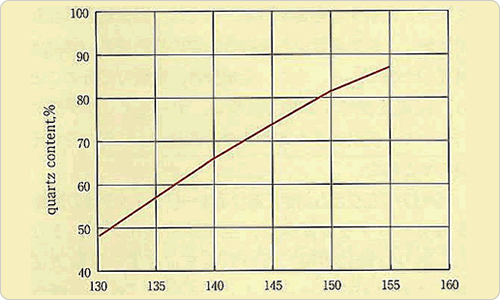
▲Specimen weight,g
Fig.14 試験片重量と石英量の関係
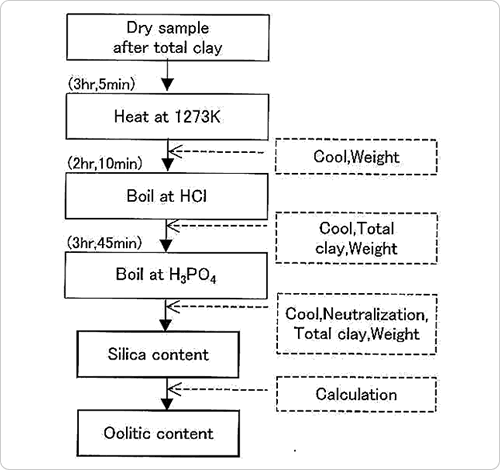
▲Fig.15 シリカプログラムのフローチャート
(測定時間,作業時間)
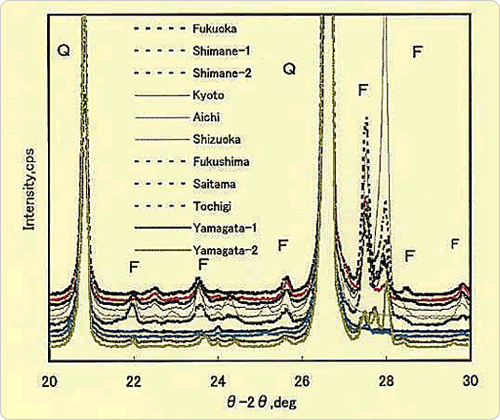
▲Fig.16 補正X線回折オーリチック試験法による石英と長石の回折チャート
Q:石英 F:長石
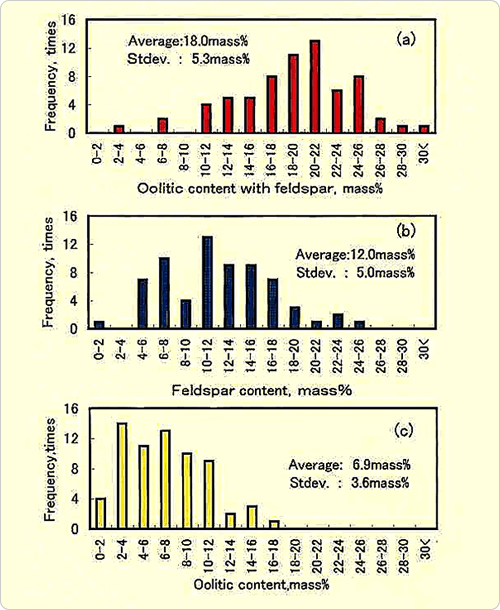
▲Fig.17 補正X線回折オーリチック試験によるオーリチック分
これらの測定は,鋳造工場より生型砂をビニール袋で頂き,数日後に弊社の試験室で測定したものである.
各々の鋳造工場の生型砂分析データをTable9と対比すれば,平均に対してどのような偏りの生型砂を使用しているか判断できる.
生型ライン構成や鋳造製品等によって,生型砂の管理値が変化するので,その偏りから理論的に妥当な生型砂かどうか判断するとよい.
なお,後述するように,オーリチック分はシリカプログラム試験ではリン酸可溶分として定量され,新のオーリチック分が測定できないので,長石を含む低耐火度 物質として表している.
Table9 1985年と2006年の生型特性の推移 |
1985 | 2006 | |||||
AVERAGE | STDEV | AVERAGE | STDEV | |||
|
38.0 | 8.5 | 29.6 | 2.2 | ||
|
1.434 | 0.050 | 1.444 | 0.028 | ||
|
11.5 | 3.6 | 16.2 | 2.2 | ||
Permeability | 147 | 43 | 137 | 17 | ||
|
82.7 | 6.3 | 76.6 | 5.9 | ||
|
3.7 | 0.9 | 2.8 | 0.3 | ||
|
11.3 | 2.1 | 9.3 | 1.4 | ||
|
8.1 | 2.1 | 7.8 | 1.1 | ||
|
3.3 | 1.3 | 3.63 | 0.72 | ||
|
115.0 | 14.2 | 111.1 | 17.8 | ||
|
2.8 | 1.3 | 3.22 | 0.74 | ||
|
1.3 | 0.6 | 0.82 | 0.22 | ||
|
1.7 | 1.8 | 0.26 | 0.44 | ||
|
20.4 | 9.0 | 21.1 | 3.1 | ||
|
65.8 | 10.0 | 67.0 | 3.3 |
■3-管理のための試験方法 |
●コンパクタビリティ(Compactability)
コンパクタビリティは,生型砂が3360μmの篩いを通過させ,φ50×110の容器に投入し,3回ラミングした試験片の高さにより,次式から計算できる.
コンパクタビリティは,生型砂が3360μmの篩いを通過させ,φ50×110の容器に投入し,3回ラミングした試験片の高さにより,次式から計算できる.
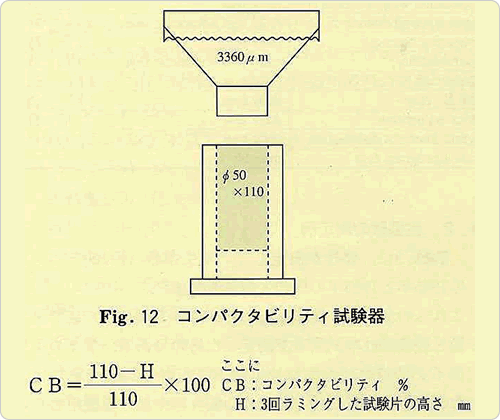
▲Fig.12 コンパクタビリティ試験器
測定方法から明らかなように,コンパクタビリティは,流動性を表す特性である.
また,コンパクタビリティは,およそ25~55%の間で水分と相関があり,Fig.13に見られる様な直線的な関係がある.
したがって,コンパクタビリティを測定することで水分を推定することができる.
ただし,これは活性粘土分,全粘土分,オーリチック分などの生型砂組成が一定の時に当てはまる.
つまり,コンパクタビリティと水分の相関が無くなる時は,生型砂組成が変化している時と判断することができる.
また,コンパクタビリティは,およそ25~55%の間で水分と相関があり,Fig.13に見られる様な直線的な関係がある.
したがって,コンパクタビリティを測定することで水分を推定することができる.
ただし,これは活性粘土分,全粘土分,オーリチック分などの生型砂組成が一定の時に当てはまる.
つまり,コンパクタビリティと水分の相関が無くなる時は,生型砂組成が変化している時と判断することができる.
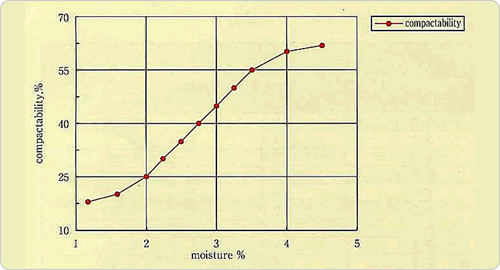
▲Fig.13 コンパクタビリティと水分の関係
コンパクタビリティは,管理値として適正な値を決める必要がある.
最近の高速・高圧造型機では,造型時に35%前後に管理する事が多い.
低圧造型機では40~50%になる.コンパクタビリティは,低い場合と高い場合で発生する問題が異なる.そのために適正な値を決める必要がある.
Table10にコンパクタビリティの変化による問題をまとめた.
●水分(Moisture)
水分は,コンパクタビリティと相関があるために,水分量の変化と鋳造欠陥の関係は,Table6と同一となる.
生型砂組成が一定の時,相関があるために,相関がなくなった時は,生型砂組成が変化したと考えればよい.
コンパクタビリティが一定であるにもかかわらず,水分が増加している場合と減少している場合の生型砂組成の変化をTable11にまとめた.
水分は生型砂の電気抵抗,密度,トルク,電磁波等から間接的に自動測定することが可能ではあるが,データをコンバートする際にエラーが生じやすい.
生型砂を乾燥して測定する方法は正確であるが,測定に時間を要する.自動測定で頻度よく測定し,1日に1度か2度乾燥による方法でチェックするとよい.
●試験片重量(密度)(Specimen weight(density))
試験片密度は,抗圧力を測定する際の試験片の密度である.試験片密度が低いことはオーリチックが増加していることを示している.その結果,焼付き(目さし)が増加し, 生型砂の水分添加量が増加する.試験片密度が高い場合は,膨張系の欠陥や砂かみ欠陥が増加する.
Fig.14に,試験片重量と石英含有量の関係を示した.
試験片重量を測定する事で石英含有量を推定する事が可能である.石英含有量は,シリカプログラム試験で正確な値を測定できる.試験片重量からの推定は,エラーが入りやすいが迅速である.
最近の高速・高圧造型機では,造型時に35%前後に管理する事が多い.
低圧造型機では40~50%になる.コンパクタビリティは,低い場合と高い場合で発生する問題が異なる.そのために適正な値を決める必要がある.
Table10にコンパクタビリティの変化による問題をまとめた.
Table10 コンパクタビリティの高低による問題 |
low level | high level |
a)sand inclusions b)mold drop c)erosion d)crush e)broken edges f)scab g)expansion defects |
a)oversize castings b)mold-wall movement c)blowholes d)pinholes e)rough surfaces f)shake-out problems g)collapsibility h)penetration i)burn on |
●水分(Moisture)
水分は,コンパクタビリティと相関があるために,水分量の変化と鋳造欠陥の関係は,Table6と同一となる.
生型砂組成が一定の時,相関があるために,相関がなくなった時は,生型砂組成が変化したと考えればよい.
コンパクタビリティが一定であるにもかかわらず,水分が増加している場合と減少している場合の生型砂組成の変化をTable11にまとめた.
Table11 生型砂組成の変動と水分の関係 |
increasing moisture | decreasing moisture |
a)increase in MB-clay b)increase in total clay c)increase in oolitics d)increase in fines e)increase in additives f)low mixing efficiency |
a)reduction in MB-clay b)reduction in total clay c)reduction in oolitics d)reduction in fines e)reduction in additives f)high mixing effeciecy |
水分は生型砂の電気抵抗,密度,トルク,電磁波等から間接的に自動測定することが可能ではあるが,データをコンバートする際にエラーが生じやすい.
生型砂を乾燥して測定する方法は正確であるが,測定に時間を要する.自動測定で頻度よく測定し,1日に1度か2度乾燥による方法でチェックするとよい.
●試験片重量(密度)(Specimen weight(density))
試験片密度は,抗圧力を測定する際の試験片の密度である.試験片密度が低いことはオーリチックが増加していることを示している.その結果,焼付き(目さし)が増加し, 生型砂の水分添加量が増加する.試験片密度が高い場合は,膨張系の欠陥や砂かみ欠陥が増加する.
Fig.14に,試験片重量と石英含有量の関係を示した.
試験片重量を測定する事で石英含有量を推定する事が可能である.石英含有量は,シリカプログラム試験で正確な値を測定できる.試験片重量からの推定は,エラーが入りやすいが迅速である.
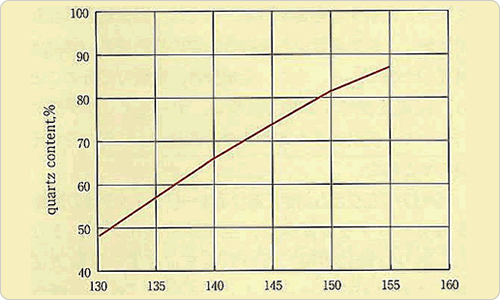
▲Specimen weight,g
Fig.14 試験片重量と石英量の関係
●抗圧力,せん断力(Green compression strength, Shearing strength)
湿態抗圧力は,生型砂の強度を代表的に表す特性である.
ベントナイト添加量が15%までは,量が増えるにしたがって抗圧力が増加する.15%以上になるとけい砂の内部摩擦応力が低下するために,抗圧力がサチレイトしそれ以上は上がらなくなる.
鋳物砂の強度発現は以下の要因から成り立っている.
(1)クーロン力(Coulomb's force)
(2)ファン・デル・ワールス力(Van der Waals' force)
(3)水の表面張力(surface tension of water)
(4)けい砂の内部摩擦応力(frictional stress of sand grain)
鋳物砂は,けい砂-ベントナイト-水の混合物であり,それらの比率は一般的には,けい砂は85~95%,ベントナイトは3~15%,水は1~7%である.これらの比率の中で,ベントナイトに対して水が20~35%の間で最も抗圧力が高くなる.また,混練効率が強度に対して重要なファクターとなる.
抗圧力の他に,鋳型の強度を測定する方法としては,せん断力,引張力ある.これらは,強度発現の要因の内,内部摩擦応力の寄与率が小さくなり,(1)~(3)のベントナイト-水の要因が高くなる.
抗圧力は(4)の寄与率が高い.抗圧力を測定すると,砂-ベントナイト-水の強度が測定でき,剪断力や引張力を測定すると,ベントナイト-水の強度を測定することになる.
●通気度(Permeability)
通気度は,試験片密度に左右される特性であり,試験片密度が上昇するにしたがって低下する.
試験片密度と通気度の間には,高い負の相関がある.
ただし,試験片密度が各生型砂組成の比重と生型砂特性の充填性の影響を受けるのに対して,湿態通気度は,生型砂 特性の充填性と鋳物砂の粒度構成の影響を受ける.
通気度の値は,一般的には120~180が主体である.通気度が低いと,ガス欠陥(ブローホール)が発生しやすくなるが,鋳肌は良好になる.
逆に通気度が高くなるとガス欠陥は少なくなるが,物理的焼付き欠陥が発生しやすくなる.
また,鋳型の熱伝導性は,空気(蒸気)を媒体として熱が伝わるので,通気度が高いと熱が伝わりやすくなる.
●全粘土分(Total clay)
全粘土分は,JIS Z 2601(鋳物砂の粘土分試験方法)によって測定できる.
この粘土分は粘土鉱物学的な粘土を指すものではなく,20μm以下の粒子を意味する.
つまり,20μm 以下の粒子であれば,ベントナイト,けい砂,澱粉,石炭粉等の微粒子を全て指す.測定はストークスの法則を利用している.
20μm以上の粒子は,水中では5分間で150mm以上沈降しない性質を利用して測定している.
●活性粘土分(Active clay,M.B.clay)
活性粘土分は,鋳物砂中のベントナイト量を直接的に求める方法である.
ベントナイトがメチレンブルー(methylen blue)を吸着することを利用した試験である.
ベントナイトは種類によって,methylen blueを吸着する量が異なり,鋳物砂のメチレンブルー吸着量を測定するとベントナイトの吸着量から計算できる.
活性粘土分を測定する際に,鋳物砂の分散方法を変えると測定値が異なってくる.
これは,ベントナイトが熱影響により結晶相関が接近しかけているからである.
強力に分散させると接近しかけたベントナイトも定量することができる.分散方法が弱いと層間の離れたベントナイトのみの定量となる.強力な分散方法とは,ピロリン酸ソーダを分散剤にして煮沸撹拌する方法である.弱い分散方法とは,硫酸を分散剤にして超音波で分散させる方法である.
●灼熱減量(Loss on ignition)
灼熱減量は,乾燥鋳物砂を1000℃で2時間焼成した時の減量パーセントである.
意味するところは,石炭粉,澱粉等の二次添加材,ベントナイト,けい砂の結晶水,中子等に含まれるバインダーなどである.
二次添加材を使用しない鋳物工場では,灼熱減量が1%前後になる.鋳物工場全体の平均は3%程度になる.
鋳物工場の砂管理者の考えによって異なるが,FCDのラインでは石炭粉を多く添加し灼熱減量を4%程度に管理するケースがある.石炭粉から発生する還元性ガスによって,ピンホールが抑制されるからである.
FCのラインでは,通常は2.5~3.0% である.灼熱減量が少ないと物理的焼付き(目さし)が発生し,多いとブローホールが発生する.
FCとFCDを交互に鋳込むラインでは,灼熱減量の設定に苦慮する.FCDにおけるピンホールの発生具合で設定値を決めている.
●粒度分布(Grain fineness distribution)
粒度分布は解粒法と団粒法がある.
解粒法は,粘土分を除去した後の鋳物砂の粒度分布である.
団粒法は,粘土分を除去しないで乾燥のみ鋳物砂に加えた後に粒度分布を測定したものである.
2つの粒度分布を対比すると粘土分の付着具合が判断できる.例えば,200mesh以降で解粒法と団粒法に差があれば,微粉状態の粘土が多いと考えられる.
また,26mesh以上でそれらの差が多いと,ダマが多いと考えられる.
湿態抗圧力は,生型砂の強度を代表的に表す特性である.
ベントナイト添加量が15%までは,量が増えるにしたがって抗圧力が増加する.15%以上になるとけい砂の内部摩擦応力が低下するために,抗圧力がサチレイトしそれ以上は上がらなくなる.
鋳物砂の強度発現は以下の要因から成り立っている.
(1)クーロン力(Coulomb's force)
(2)ファン・デル・ワールス力(Van der Waals' force)
(3)水の表面張力(surface tension of water)
(4)けい砂の内部摩擦応力(frictional stress of sand grain)
鋳物砂は,けい砂-ベントナイト-水の混合物であり,それらの比率は一般的には,けい砂は85~95%,ベントナイトは3~15%,水は1~7%である.これらの比率の中で,ベントナイトに対して水が20~35%の間で最も抗圧力が高くなる.また,混練効率が強度に対して重要なファクターとなる.
抗圧力の他に,鋳型の強度を測定する方法としては,せん断力,引張力ある.これらは,強度発現の要因の内,内部摩擦応力の寄与率が小さくなり,(1)~(3)のベントナイト-水の要因が高くなる.
抗圧力は(4)の寄与率が高い.抗圧力を測定すると,砂-ベントナイト-水の強度が測定でき,剪断力や引張力を測定すると,ベントナイト-水の強度を測定することになる.
●通気度(Permeability)
通気度は,試験片密度に左右される特性であり,試験片密度が上昇するにしたがって低下する.
試験片密度と通気度の間には,高い負の相関がある.
ただし,試験片密度が各生型砂組成の比重と生型砂特性の充填性の影響を受けるのに対して,湿態通気度は,生型砂 特性の充填性と鋳物砂の粒度構成の影響を受ける.
通気度の値は,一般的には120~180が主体である.通気度が低いと,ガス欠陥(ブローホール)が発生しやすくなるが,鋳肌は良好になる.
逆に通気度が高くなるとガス欠陥は少なくなるが,物理的焼付き欠陥が発生しやすくなる.
また,鋳型の熱伝導性は,空気(蒸気)を媒体として熱が伝わるので,通気度が高いと熱が伝わりやすくなる.
●全粘土分(Total clay)
全粘土分は,JIS Z 2601(鋳物砂の粘土分試験方法)によって測定できる.
この粘土分は粘土鉱物学的な粘土を指すものではなく,20μm以下の粒子を意味する.
つまり,20μm 以下の粒子であれば,ベントナイト,けい砂,澱粉,石炭粉等の微粒子を全て指す.測定はストークスの法則を利用している.
20μm以上の粒子は,水中では5分間で150mm以上沈降しない性質を利用して測定している.
●活性粘土分(Active clay,M.B.clay)
活性粘土分は,鋳物砂中のベントナイト量を直接的に求める方法である.
ベントナイトがメチレンブルー(methylen blue)を吸着することを利用した試験である.
ベントナイトは種類によって,methylen blueを吸着する量が異なり,鋳物砂のメチレンブルー吸着量を測定するとベントナイトの吸着量から計算できる.
活性粘土分を測定する際に,鋳物砂の分散方法を変えると測定値が異なってくる.
これは,ベントナイトが熱影響により結晶相関が接近しかけているからである.
強力に分散させると接近しかけたベントナイトも定量することができる.分散方法が弱いと層間の離れたベントナイトのみの定量となる.強力な分散方法とは,ピロリン酸ソーダを分散剤にして煮沸撹拌する方法である.弱い分散方法とは,硫酸を分散剤にして超音波で分散させる方法である.
●灼熱減量(Loss on ignition)
灼熱減量は,乾燥鋳物砂を1000℃で2時間焼成した時の減量パーセントである.
意味するところは,石炭粉,澱粉等の二次添加材,ベントナイト,けい砂の結晶水,中子等に含まれるバインダーなどである.
二次添加材を使用しない鋳物工場では,灼熱減量が1%前後になる.鋳物工場全体の平均は3%程度になる.
鋳物工場の砂管理者の考えによって異なるが,FCDのラインでは石炭粉を多く添加し灼熱減量を4%程度に管理するケースがある.石炭粉から発生する還元性ガスによって,ピンホールが抑制されるからである.
FCのラインでは,通常は2.5~3.0% である.灼熱減量が少ないと物理的焼付き(目さし)が発生し,多いとブローホールが発生する.
FCとFCDを交互に鋳込むラインでは,灼熱減量の設定に苦慮する.FCDにおけるピンホールの発生具合で設定値を決めている.
●粒度分布(Grain fineness distribution)
粒度分布は解粒法と団粒法がある.
解粒法は,粘土分を除去した後の鋳物砂の粒度分布である.
団粒法は,粘土分を除去しないで乾燥のみ鋳物砂に加えた後に粒度分布を測定したものである.
2つの粒度分布を対比すると粘土分の付着具合が判断できる.例えば,200mesh以降で解粒法と団粒法に差があれば,微粉状態の粘土が多いと考えられる.
また,26mesh以上でそれらの差が多いと,ダマが多いと考えられる.
5.シリカプログラム(Silica program)
■1-シリカプログラム試験における用語の意味 |
シリカプログラムは生型砂組成を測定する試験方法であり,通常,化学分析によりシリカ分を定量し,他の項目を計算によって算出している.
Fig.15にこの試験方法のフローチャートを示す.Table12にシリカプログラムの項目を示す.
シリカプログラム試験をすることで生型砂組成が明確になり,生型砂の管理が容易になるが,シリカプログラム試験ではシリカ分以外は全て計算値になるので,その算出方法と用語の意味を十分に理解する必要がある.
例えは,炭素質とは全炭素量では無く,灼熱減量から無機質物質の灼熱減量(結 晶水)を補正した値である.
また,金属分は,塩酸可溶分のことであり,鉄分を意味する物ではない.
オーリチック分の意味についても混乱が多々あるので,Table12にあわせてその定義をまとめた.
Fig.15にこの試験方法のフローチャートを示す.Table12にシリカプログラムの項目を示す.
シリカプログラム試験をすることで生型砂組成が明確になり,生型砂の管理が容易になるが,シリカプログラム試験ではシリカ分以外は全て計算値になるので,その算出方法と用語の意味を十分に理解する必要がある.
例えは,炭素質とは全炭素量では無く,灼熱減量から無機質物質の灼熱減量(結 晶水)を補正した値である.
また,金属分は,塩酸可溶分のことであり,鉄分を意味する物ではない.
オーリチック分の意味についても混乱が多々あるので,Table12にあわせてその定義をまとめた.
Table12 シリカプログラム試験項目とその意味 |
項 目 | 計算法あるいは用語の意味 |
炭素質(Carbonaceous materials) | 灼熱減量- (けい砂及びベントナイトの灼熱減量) |
金属分(Metallics) | 塩酸可溶分 |
不活性微粉(Inert fines) | 全粘土分-活性粘土分+炭素質+金属分 |
オーリチック分(oolitic materials) | りん酸可溶分 (基礎砂のりん酸可溶分で補正) |
シリカ分(Quartz content) | 実測値(乾燥生型砂中のシリカ分) |
フラックス分(Fluxing materials) | オーリチック分+不活性微粉 |
清浄度(Percentage cleanliness) | 全粘土分除去後の水洗砂中のシリカ分 |
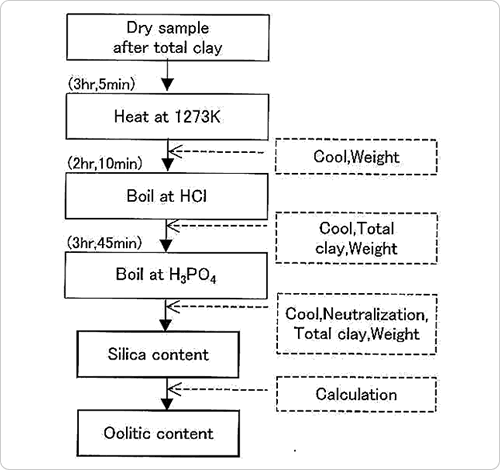
▲Fig.15 シリカプログラムのフローチャート
(測定時間,作業時間)
■2-化学分析シリカプログラム試験におけるオーリチック分の定義 |
シリカプログラム試験は,生型砂を熱リン酸により溶解し,これに溶解しない石英を定量し,基礎砂と称される新砂のオーリチック分相当で補正してオーリチック分を求める試験方法である.
ところが,この熱リン酸可溶分(低耐火度物質)を慣例的にオーリチック分と呼ぶことが多く,これが混乱の元となっている.
熱リン酸可溶分(低耐火度物質)=オーリチック分+長石
基礎砂による補正は,鋳造工場が様々なけい砂を不特定の比率で使用することで,補正ができなくなっている.
代表的なけい砂のオーリチック分相当(長石等)を,Table13に示す.けい砂の種類によって,オーリチック分相当は大きく異なる.
ところが,この熱リン酸可溶分(低耐火度物質)を慣例的にオーリチック分と呼ぶことが多く,これが混乱の元となっている.
熱リン酸可溶分(低耐火度物質)=オーリチック分+長石
基礎砂による補正は,鋳造工場が様々なけい砂を不特定の比率で使用することで,補正ができなくなっている.
代表的なけい砂のオーリチック分相当(長石等)を,Table13に示す.けい砂の種類によって,オーリチック分相当は大きく異なる.
Table13 代表的なけい砂のオーリチック分相当(長石) % |
灼熱減量 | 全粘土分 | 金属分 | オーリチック 相当 |
シリカ分 | |
再生砂 | 0.1 | 0.4 | 0.5 | 10.8 | 87.8 |
温泉津けい砂 | 0.4 | 0.1 | 0.4 | 12.9 | 86.1 |
河村けい砂-1 | 0.6 | 0.1 | 0.8 | 26.3 | 71.6 |
河村けい砂-2 | 0.7 | 0.5 | 0.9 | 27.8 | 69.0 |
最上けい砂 | 0.4 | 0.2 | 0.1 | 16.0 | 85.1 |
秩父けい砂 | 0.6 | 0.4 | 1.5 | 5.3 | 93.2 |
浜岡けい砂 | 1.1 | 0.4 | 3.5 | 54.2 | 42.4 |
白銀けい砂 | 0.2 | 0.2 | 0.2 | 2.4 | 97.1 |
三河けい砂 | 0.2 | 0.4 | 0.4 | 5.4 | 93.4 |
フラタリー | 0.1 | 0.1 | 0.2 | 0.9 | 98.6 |
フリーマントル | 0.1 | 0.1 | 0.1 | 0.5 | 99.5 |
■3-補正X線回折オーリチック試験法 1,2) |
従来のシリカプログラム分析では,オーリチック分と長石の分離定量が難しいことから,筆者らはX線回折を用いて,同一の生型砂の石英量と長石量を求め,オーリチックを計算する方法を確率している.
Fig.16にX線回折によるけい砂の石英と長石の回折チャートを示す.
オーリチックはガラス状物質であるために,X線の回折が生じないが,石英及び長石は鉱物であるために回折ピークが生じる.
これらを定量することで,生型砂中の石英量と長石量を知ることが可能である.
Fig.16にX線回折によるけい砂の石英と長石の回折チャートを示す.
オーリチックはガラス状物質であるために,X線の回折が生じないが,石英及び長石は鉱物であるために回折ピークが生じる.
これらを定量することで,生型砂中の石英量と長石量を知ることが可能である.
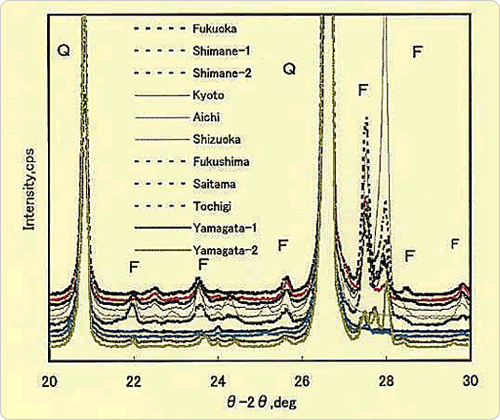
▲Fig.16 補正X線回折オーリチック試験法による石英と長石の回折チャート
Q:石英 F:長石
Fig.17に補正X線回折オーリチック試験によって求めた生型砂のオーリチック分を示す.
あわせて,低耐火度物質(長石を含むオーリチック)と長石を示す.
オーリチック分は6.9%が平均であり,およそ2~12%の範囲に多く分布していることが明らかとなっている.
あわせて,低耐火度物質(長石を含むオーリチック)と長石を示す.
オーリチック分は6.9%が平均であり,およそ2~12%の範囲に多く分布していることが明らかとなっている.
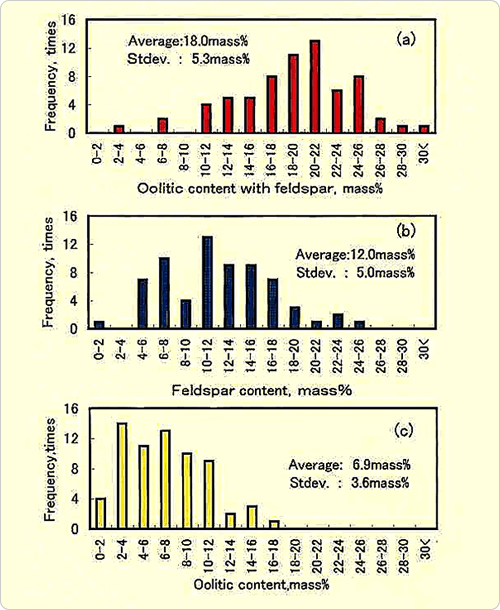
▲Fig.17 補正X線回折オーリチック試験によるオーリチック分
6.結 言
本編は,1998年10月に発行したTSUCHIYOSHI技術NEWSの技術論文を当社のホームページにアップするに当たり改訂したものである.
いささか古くなったデータや時代の流れにそぐわない箇所を書き改めた.
前回同様に,生型型材料とその試験方法に関する基礎レベルの内容としてまとめている.
生型試験方法及び測定の例については,弊社の生型分析結果報告書(鋳造工場の生型砂を弊社で分析)の項目順に準拠して記述しているので対比して見ていただければ幸いである.
【参考文献】
1) 太田英明:鋳型の生産技術(素形材センター)(1995)15
2) D.M.Stefanescu,S.R.Giese,T.S.Piwonka,A.M.Lane:AFS Trans.104(1996)1233
3) R.E.Grim:Clay Mineralagy(McGRAW-HILL)(1968)79
4) R.E.Grim:Applied Clay Mineralogy(McGRAW-HILL)(1962)181
5) 鈴木繁男,田村太郎,二木邦夫:鋳型用澱粉(日本綜合鋳物センター)(1996)18
6) 黒川豊,尾添伸明,太田英明:鋳造工学70(1998)7,495
7) H.W.Dietert,A.L.Graham,R.Piaski,F.Hofmann:AFS Trans.83(1975)233
8) F.Hofmann,F.Satmar:AFS Trans.88(1980)177
9) 黒川豊,市岡雅義,太田英明,三宅秀和:鋳造工学71(1999)614
10) 黒川豊,水田豊昭,矢尾井潤,太田英明,三宅秀和:鋳造工学72(2000)346
11) 黒川豊,矢尾井潤,上林仁司,太田英明,三宅秀和:鋳造工学73(2001)187
いささか古くなったデータや時代の流れにそぐわない箇所を書き改めた.
前回同様に,生型型材料とその試験方法に関する基礎レベルの内容としてまとめている.
生型試験方法及び測定の例については,弊社の生型分析結果報告書(鋳造工場の生型砂を弊社で分析)の項目順に準拠して記述しているので対比して見ていただければ幸いである.
【参考文献】
1) 太田英明:鋳型の生産技術(素形材センター)(1995)15
2) D.M.Stefanescu,S.R.Giese,T.S.Piwonka,A.M.Lane:AFS Trans.104(1996)1233
3) R.E.Grim:Clay Mineralagy(McGRAW-HILL)(1968)79
4) R.E.Grim:Applied Clay Mineralogy(McGRAW-HILL)(1962)181
5) 鈴木繁男,田村太郎,二木邦夫:鋳型用澱粉(日本綜合鋳物センター)(1996)18
6) 黒川豊,尾添伸明,太田英明:鋳造工学70(1998)7,495
7) H.W.Dietert,A.L.Graham,R.Piaski,F.Hofmann:AFS Trans.83(1975)233
8) F.Hofmann,F.Satmar:AFS Trans.88(1980)177
9) 黒川豊,市岡雅義,太田英明,三宅秀和:鋳造工学71(1999)614
10) 黒川豊,水田豊昭,矢尾井潤,太田英明,三宅秀和:鋳造工学72(2000)346
11) 黒川豊,矢尾井潤,上林仁司,太田英明,三宅秀和:鋳造工学73(2001)187